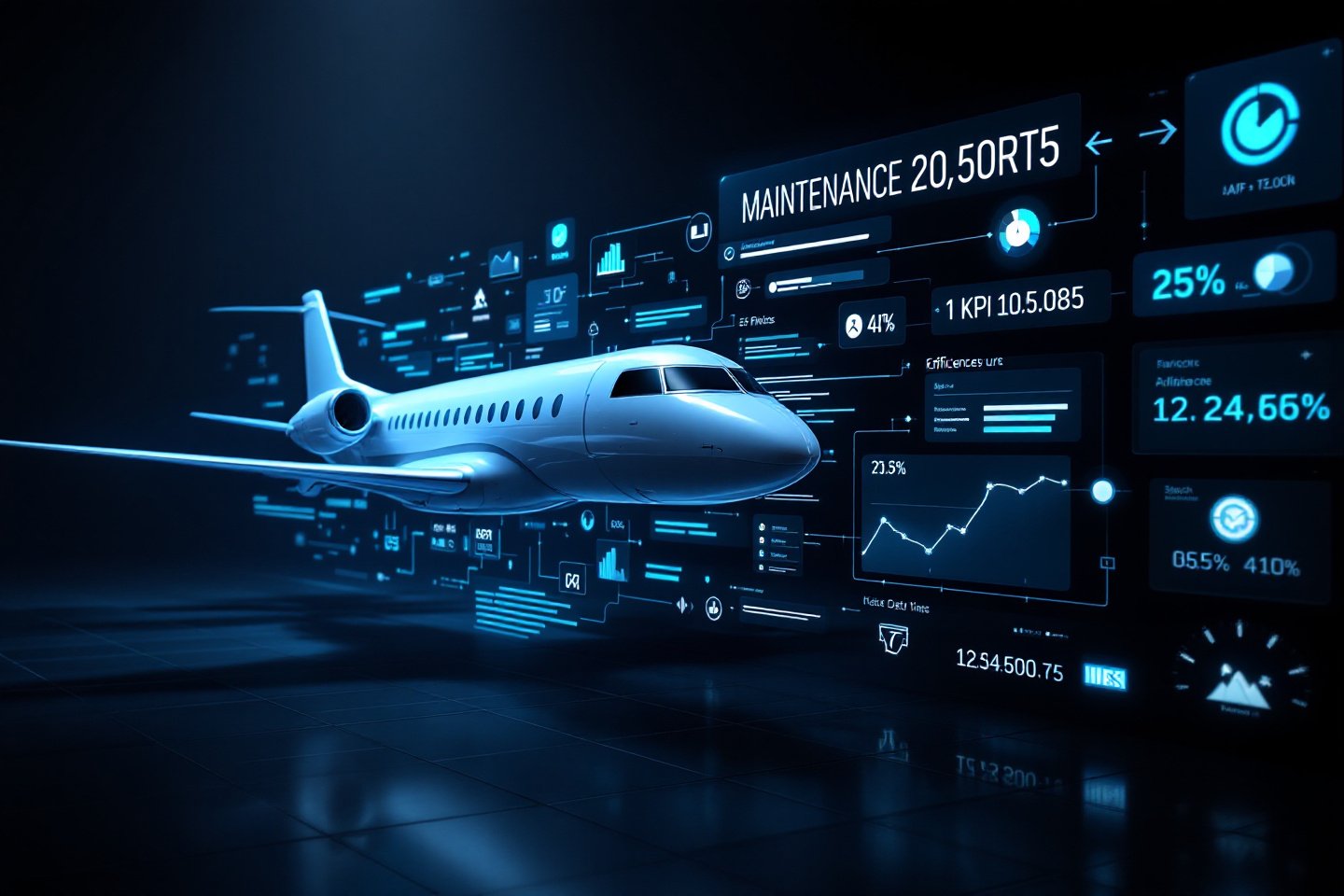
Digital Twin, Business Process (BPM) & Continuous Improvement Program
Digital Twin, Business Process (BPM) & Continuous Improvement Program
A cutting-edge solution designed to replicate and enhance your operational processes through digital simulation and ongoing optimization
Tests out new ideas in a safe and controlled environment
Creates virtual replicas of physical objects or systems
Monitors and analyzes real-world objects in real-time
Identify potential issues before they become major problems
Improved Efficiency
Reduced Costs
Increased Safety
Decision Making
Enhanced Customer Experience
Improved Innovation
Features
Ensure key business processes are utilizes the maximum capabilities of existing technologies
Optimize MRO workflows through virtual simulation, reducing trial-and-error in physical processes
Continuously improve operational processes by leveraging data-driven insights
Identify root causes and solve systemic issues from Goods-in to Goods-out
Facing any of these Challenges?
Pain Points
Inefficient Repair Workflow due to Lack of Methodization
MROs often lack a structured process for methodizing their repair workflow to maximize efficiency. Without such a process, there is a missed opportunity to streamline operations, reduce costs, and improve the overall effectiveness of repair processes.
Searching for Tools Impacting Shopfloor Efficiencies
Technicians in MROs often spend significant time searching for tools on the shopfloor, which can result in significant delays of 30 minutes to 1 hour per work order. These inefficiencies directly impact customer turnaround times and have the potential to lead to delays and customer dissatisfaction, affecting operational overall efficiencies.
Manual Data Entry in Shipping and Receiving
A significant portion of units lack QR codes or integrations with customer systems, necessitating manual data input into the ERP (Entreprise ressource planning). This manual process is susceptible to human errors and imposes substantial administrative burden on MRO operations.
Solutions
Develop a standardized and methodized repair workflow that optimizes efficiency, reduces operational costs (eg. PMA), eliminate waste, and enhances overall repair process effectiveness.
Implement a digital tool tracking and management system that utilizes RFID technology and real-time location tracking to provide technicians with the precise location of tools on the shopfloor. The solution can also enable proactive alerts and notifications to streamline the maintenance and calibration process.
Implement automated data capture solutions, such as barcode scanning or RFID, to eliminate manual data entry, auto-populate repair order information directly from the vendor and/or customer, and improve data accuracy in shipping and receiving.